Les bancs de test pour le suivi qualité en production
Dans une phase initiale de spécification d’un produit ou de son chiffrage associé, on pense principalement études (mécanique, électronique), développement logiciel, conception et réalisation des outillages divers, prototypes, préséries.
Parfois, la certification est mentionnée mais très souvent la phase de développement des bancs de test est oubliée car il est difficile de prévoir ce qu’elle implique, coûte en ressources et en matériels. De plus, le calendrier de développement est souvent très serré et les clients demandent de tenir absolument le « Go To Market » du produit. Il en ressort que les tests sont souvent écartés du processus car ils sont perçus comme une étape qui prend du temps et ralentit le développement.
Cependant, cette étape est clé pour garantir que vos produits sortiront de production conformes à votre cahier des charges et avec le niveau de qualité requis. Un produit non conforme parti de vos chaînes de fabrication coûte cher à réparer ou à remplacer et écorne votre réputation chez votre distributeur ou votre client final.
Design for Test
Il faut penser à la stratégie de test qualité le plus tôt possible dans la conception du produit afin de s’assurer que le produit sera testable et qu’il sera possible de mettre en œuvre la séquence de tests fonctionnels à effectuer en production et s’assurer que le produit est fiable dans le temps sans dérive au fil des lots de fabrication.
Dans la phase de conception, il est important de définir à partir de la schématique les éléments essentiels à vérifier soit lors de la qualification, soit en production série. Il faut alors implémenter des points de test sur le circuit imprimé (PCB) accessibles pour les divers moyens à mettre en œuvre (pointes de touches d’instruments de mesure, connecteurs, pointes de test sur lits à clous). Ils seront utiles pour connecter les bancs de test à la carte électronique.
Il faut aussi tenir compte pour cela des conditions d’utilisation des produits (température, type et qualité d’alimentation par exemple) pour définir les équipotentielles à surveiller et à mesurer afin de s’assurer du bon fonctionnement du produit dans toutes ses plages d’utilisation.
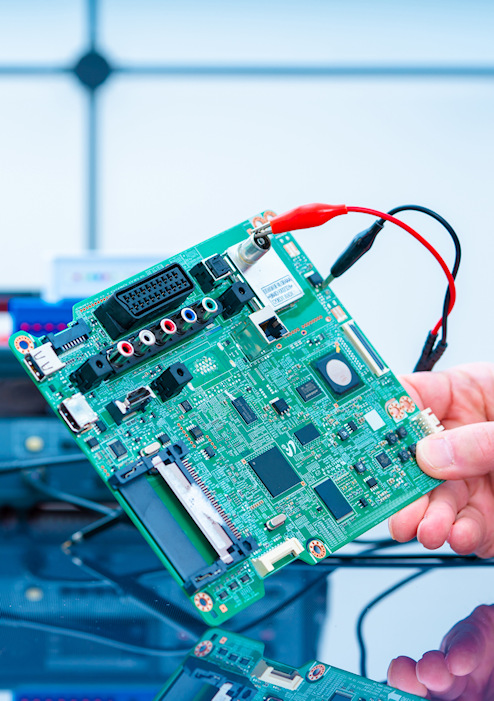
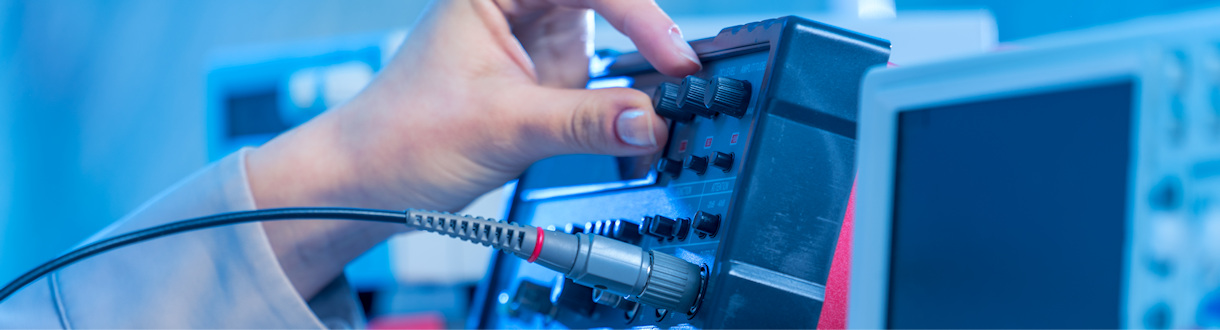
Qualification
La qualification du produit intervient à plusieurs stades de la conception et industrialisation.
Tout d’abord, lors de la conception, il faut s’assurer du bon fonctionnement de l’architecture produit en vérifiant et calculant les compatibilités des signaux de sortie et d’entrée des divers blocs fonctionnels du produit. Il faut aussi calculer de façon théorique la consommation énergétique du produit, qui plus est, s’il est autonome en énergie.
Lors des phases prototypes EVT/DVT, ces données sont corrélées avec des mesures faites sur les produits fabriqués et cela dans toutes les plages de température et d’alimentation. Il faut vérifier que la réponse des composants est conforme aux spécifications desdits composants et que la fonction électronique complète répond au besoin exprimé et au fonctionnement souhaité.
C’est à cette étape qu’on démarre la spécification de test fonctionnel en production pour le développement des bancs de test électronique.
En phase de présérie, une qualification complémentaire sur un nombre plus conséquent de pièces est réalisée afin de confirmer les mesures et calculer la dispersion des fonctions électroniques. Ces mesures permettront de compléter la spécification de test fonctionnel en intégrant les marges d’acceptation des tests automatiques faits en production.
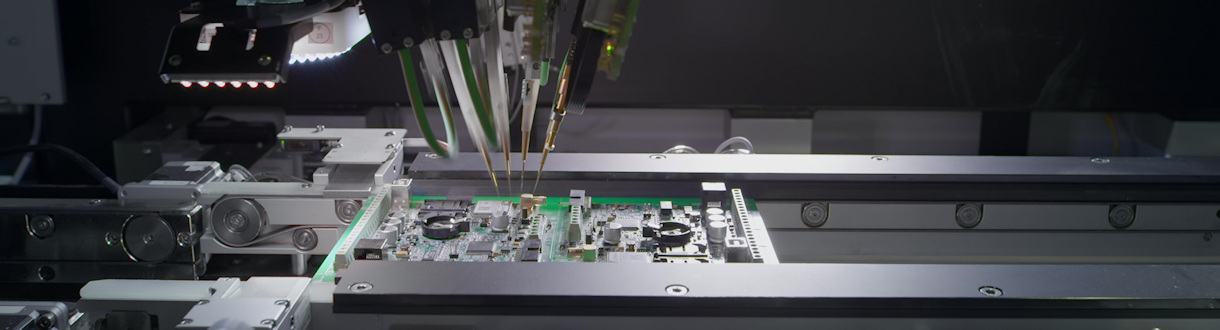
Les divers bancs de test en production
Les tests en production permettent de différentier les produits réputés corrects des produits présentant un défaut et refusés.
Différents types de tests peuvent être effectués sur un produit avant sa fabrication finale. Ils comprennent des tests électroniques au niveau in situ, fonctionnel, et de sécurité.
Tests in situ : le test In Situ consiste à tester les composants d’une carte électronique et de s’assurer qu’il ne manque pas de composants sur la carte, qu’il n’y a pas de courts circuits et qu’ils sont convenablement soudés. Un test complémentaire de contrôle optique permet de regarder la qualité mécanique des soudures et éviter des soudures sèches qui pourraient provoquer une panne ultérieure et rendre le produit inopérant lors de son exploitation.
Tests fonctionnels : des bancs de test électroniques (comprenant des instruments de mesure et un séquenceur logiciel) sont assemblés pour vérifier si les blocs matériels et logiciels fonctionnent correctement ensemble. Ils servent également à vérifier les éventuels problèmes dans l’architecture système ou problèmes d’interaction entre les composants. On s’appuie sur la spécification de test fonctionnel développée lors des phases prototypes et complétée lors de la phase présérie.
Il faut souvent développer un firmware produit spécifique de test afin de pouvoir tester la totalité des fonctions du produit.
Tests de sécurité : ces tests permettent de s’assurer que le produit est conforme aux réglementations en vigueur en fonction du ou des pays où le produit sera commercialisé.
Cette phase de test fonctionnel est clé dans le processus de contrôle qualité du produit car elle va permettre de trouver les produits défectueux avant la mise en carton et l’expédition.
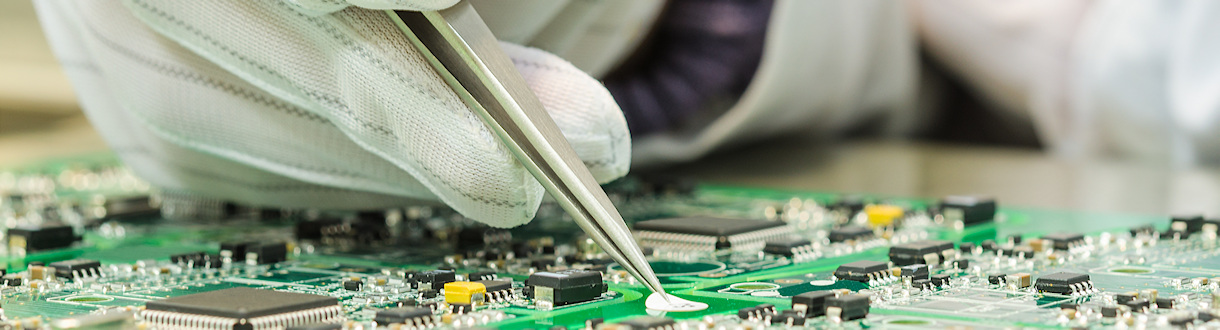
Traçabilité et test qualité
Le banc de test fonctionnel va stocker les mesures réalisées sur tous les produits fabriqués. Il va émettre des rapports sur chacun d’entre eux à travers leur numéro de série individuel.
Il va aussi permettre de réaliser une traçabilité des produits en y ajoutant des informations complémentaires comme la version du produit, son jour d’assemblage, le jour de test, les dates et adresses d’expédition, des numéros de lots de certains composants, des identifiants individuels de composants, des adresses MAC de composants radio, etc.
Le banc de test génère alors des étiquettes avec les informations légales de traçabilité : CE, RoHs, numéro de série, logo et adresse du fabricant. Grâce à ce système de traçabilité, nous pouvons savoir pour un produit son jour d’assemblage et le jour de test, mais aussi isoler un défaut possible à un lot de fabrication.
Ces informations seront très utiles pour le service après-vente du client.
Vous avez un projet ?
Les équipes de TXCube vous apportent leur expérience sur la meilleure façon de répondre à vos enjeux.