Product design
Product design is not just about making the product look beautiful. You need to make sure the product does what it needs to do, and it does it better than other models.
The best way to design a product is to think about how end customers will use it, then consider the most effective way to design it for easy use.
You need to know your end customer’s habits and your market. What are they looking for? How do they feel when they see the product? What are they afraid of if they use your product incorrectly? What is the perceived quality desired? What are the expected sales quantities? What is the price positioning required?
Answering these questions will help you to define a specification according to the needs before entering the product design phase. Once you have identified your users’ needs and market expectations, you can begin to consider how best to meet those needs, incorporating economic and industrial constraints.
The industrial design phase
Industrial design is a process that begins with an idea for a product or system and culminates with a prototype development.
The process of designing a mechatronic assembly involves three main steps:
- Prototype Design – This step involves creating 3D models from 2D drawings using CAD (Computer-Aided Design).
- Industrial Design – In this step, designers create a CAD model that meets various industry standards and specifications. This includes considering factors such as ergonomics, aesthetics and fabricability.
- Production Design – In this phase, designers develop a manufacturing process diagram that shows how each part will be manufactured during the project’s production steps.
During this phase, our team will assist you in writing the product specifications that will serve as the reference document for designing your product.
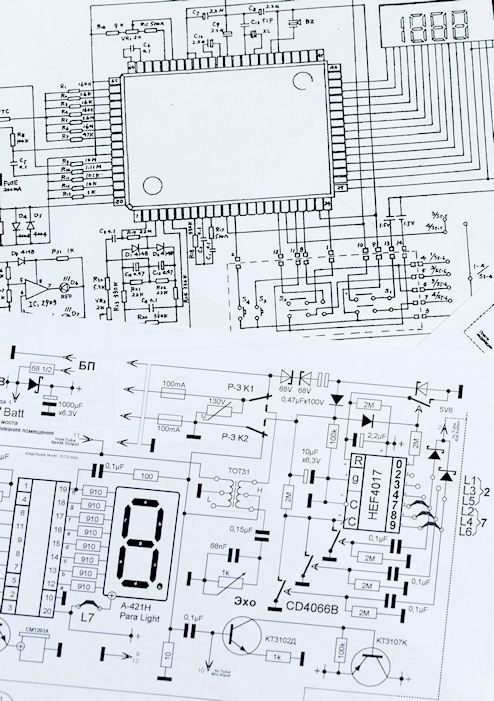
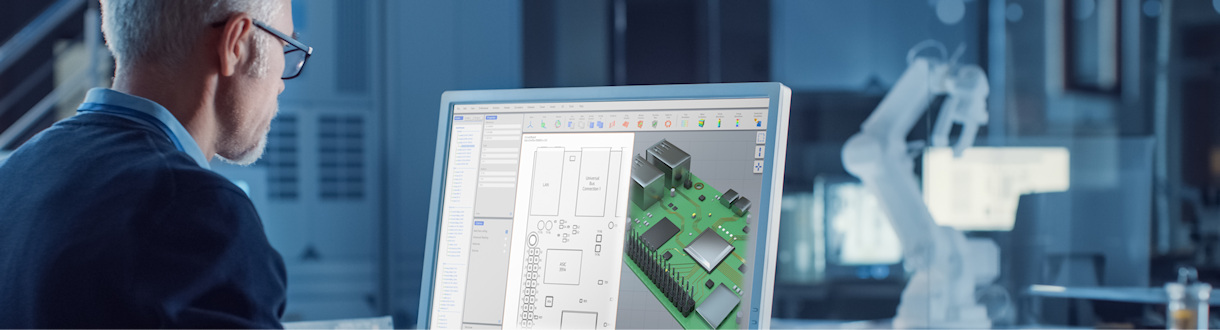
Design to Cost
Many products are designed without placing the concept of cost at the center of the project. Once the development is well advanced or completed, we realize that the cost is too high, the market price fixed and therefore the margins are too low to be profitable. It is then necessary to redesign everything with a very strong impact on the product launch schedule [Time to Market] or to keep a product with low margin, knowing that margins shrink as the product’s market appeal diminishes over time. Design to Cost involves several steps.
You must know your target selling price and deduct your cost from it, taking into account your marketing costs, sales channels and business structure costs. This process helps you to understand the margin needed for the success of your project and therefore the profitability of your company.
Design to Cost is a mindset and approach that must be adopted by the whole organization, from the design office to the purchasing through production and supply chain. It is a tool that allows us to focus on the essential, optimizing and challenging the current product definition.
The goal is to produce a product of equal or greater quality at a lower cost. This is achieved by identifying improvement opportunities in key areas such as sourcing, manufacturing processes, assembly processes and material costs.
We must constantly keep in mind: sourcing, production, industrialization and supply chain when designing the product to achieve a high-performance Design to Cost.
TXCube has assisted many companies in this area, both during initial design and in technical redesigns of products.
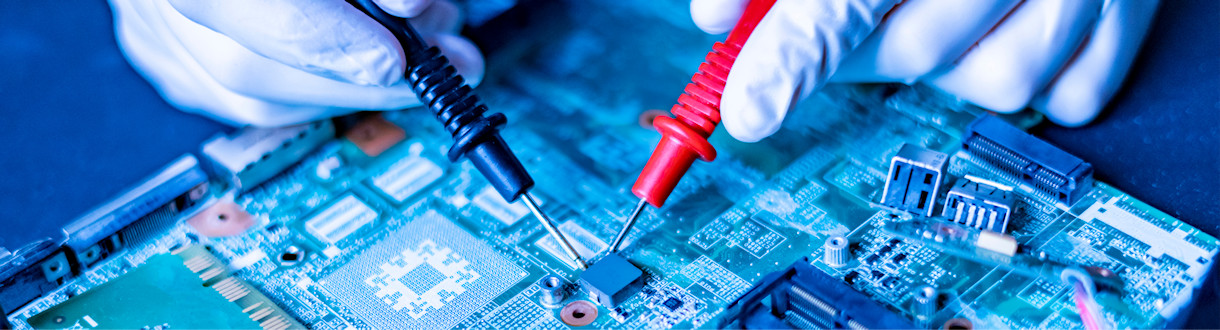
Design for Test
Because the development schedule is often very tight and customers ask for faster and cheaper solutions, testing is often left out of the process, being seen as a time-consuming and slow-moving step. The result is less reliable, less quality and less cost-effective products than they should be.
It is crucial to consider the testing strategy as early as possible in the product design to ensure that the product will be reliable over time. The purpose of Design for Test is to ensure that a product meets its requirements and complies with all applicable regulations. Therefore, various aspects of a product must be considered before testing to ensure that it meets the design specifications.
One aspect to consider in product design is user interaction. Some products are designed for simple interactions, such as pressing buttons or switches, while others require more complex interactions, or need to operate in stressful environments (temperature, shocks, humidity, etc.).
This can be a complex task for new products, but anticipating these aspects from the start of the project makes it easier to design the product and ensure its proper functioning once on the market.
In parallel with the so-called production tests, the product must also be qualified. Different types of tests can be performed on a product before it is manufactured. These tests include functional, and security tests.
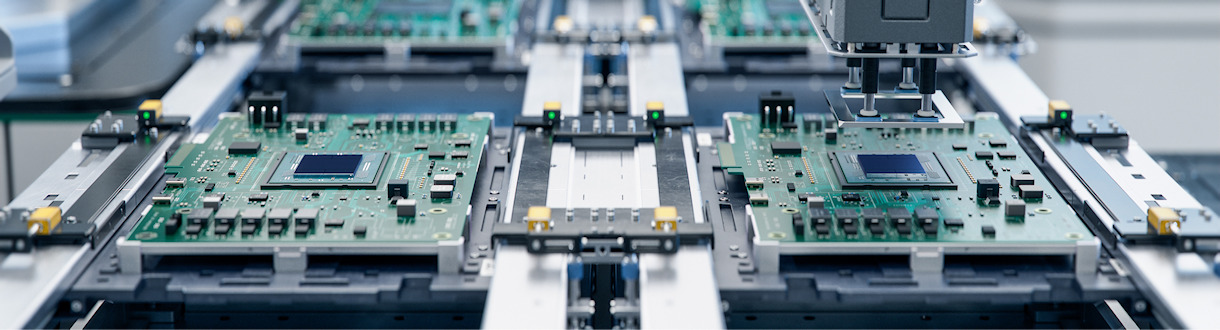
Design for Manufacturing
Design for Manufacturing (DFM) is a pre-production process aimed at reducing the complexity of electronic or mechanical manufacturing through efficient design and careful part selection. This design approach ensures that your final product will be cost-effective, easy to produce and reliable over time.
Design for Manufacturing is a comprehensive design methodology that focuses primarily on identifying and eliminating potential manufacturing problems through optimized placement and routing of parts, and the provision of efficient assembly models to enable all production processes to be completed in a timely and cost-effective manner.
In many cases, the manufacturing process is decided before the design of the PCB or mechanical part is completed. Therefore, it is important to consider DFM from the beginning of the project. This way, you can avoid potential issues that could become costly if they are discovered too late during the design.
During the Design for Manufacturing process, engineers identify potential risks and problems that may arise during the production process.
DFM analyzes the entire manufacturing process, from material selection to the assembly process, to optimize the design for the most efficient production cycle. The DFM process is an essential part of the product development cycle for any manufacturer of electronics and/or mechanical parts. By analyzing and optimizing the Design for Manufacturing, engineers can ensure that the final product is cost-effective, easy to produce and reliable over time.
Got a project ?
TXCube brings the experience on the best way to meet your challenges. So, don’t wait and